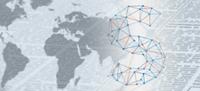
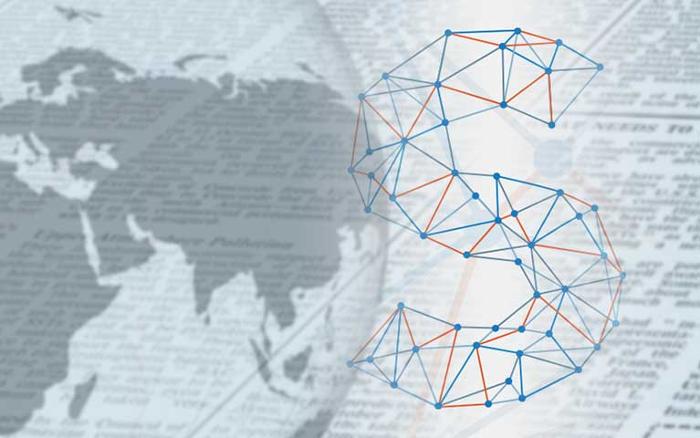
OROEL Promotes Recycling of Raw Materials in Protective Clothing

OROEL will be at SICUR to present its new strategy to become the first industrial garment manufacturing company to develop and implement a circular economy integration plan. The plan aims to reduce its use of virgin raw materials and waste production. It also aims to reduce pollution, starting from the design phase and consider the environmental impact of a product throughout its lifetime. It will increase the useful lifespan of products and encourage reuse, repair and refurbishment. It will also increase recovery and recycling and minimise the use of new raw materials. Read more
This year at SICUR, OROEL will be celebrating its 40th birthday and presenting its new business strategy. The company began in 1980, and its business has kept on evolving and adapting ever since. Now, at the dawn of the 2020s, it is bringing PPE, and particularly the protective clothing market, into the circular economy. The new strategy aims to reduce use of virgin raw materials and waste production. For OROEL, SICUR 2020 is a place to present different content and the major changes underway at the company, which is celebrating its 40th birthday, with the following milestones:
1980: The Company was founded, and in its first decade it manufactured work clothes and uniforms in general for different industrial sectors. “In this decade, we were already manufacturing protective clothing that, although not PPE, was already used as such. One of our main products was fire-resistant clothing for the forest fire-fighting crews of ICONA (Nature Conservation Institute) and various autonomous regions.”
1990: “We became a member of Asepal (Association of PPE Manufacturers) and transformed into a protective clothing manufacturing company. We were the first Spanish company to certify our apparel for heat and fire resistance. In this decade, we became Spain’s leading protective clothing manufacturer.”
2000: “Once we had consolidated our position as the leading manufacturer of protective clothing, Oroel started on a new path: the renting, leasing and maintenance of protective clothing for industrial clients. In 2004, we set up a production line in Tangiers (Morocco), and moved the garment manufacturing there.”
2010: “After the 2008 economic crisis we understood that we needed to go out and sell to markets abroad. In 2010 we began our expansion into European and South American markets. In 2013 we opened an office in Colombia, Oroel Colombia.”
Towards Sustainability
Over its forty-year history, the company has always been respectful of people, animals, nature and the environment. “As we all know, over the last ten years, there’s been a surge in social awareness about the need to protect the planet from the great threat that climate change represents. That’s why we’ve been working over the last few years on how we can contribute to improving this.”
Oroel aims to be the first industrial apparel manufacturer to develop and implement a plan for integration with the Circular Economy. “Out of conviction, because we believe that we must build a sustainable and forward-looking company.” To achieve this, we’ve developed a working plan with short-, medium- and long-term strategies. “We began this decade in 2020 by presenting our strategy and moving the PPE market, and specifically the protective clothing market, into the Circular economy. Based on the circular economy strategy, which aims to reduce the use of virgin raw materials and waste production.” So, we are going to:
-
Reduce polluting waste starting from the design phase and consider the environmental impact of a product throughout its lifetime.
-
Increase the useful lifetime of our products: Reuse. Repair. Refurbish.
-
Increase recovery and recycling, minimising the use of new raw materials.
-
Make efficient use of natural resources and avoid or minimise our use of non-renewable resources.
-
Recover protective garments from customers who request it.
-
Use special machines to shred manufacturing waste and garments that have reached the end of their life cycle. Then transform the waste into recycled fibre by making textile flock. With this process, we can make recycled fibre yarn.
-
And from that yarn, we make new fabric and then make garments to supply our customers.
-
We expect this process to give us major savings in our consumption of virgin raw materials, water, electricity and other energy.
According to A New Textiles Economy (2018)
-
The production of 1 kg of cotton garments uses up to 3 kg of chemicals.
-
Textiles production (including cotton farming) uses almost 100 billion cubic metres of water annually, representing 4% of global freshwater withdrawal.
-
The equivalent of more than 3 trillion 0.5 litre PET bottles is needed to produce plastic-based clothes every year.
Other practices we will be implementing include:
-
Switching from plastic bags to wrap garments to compostable, biodegradable bags. Until more environmentally-friendly materials become available.
-
Switching from plastic hangers to others made of wood or recycled plastic.
-
Stopping using plastic bags for brochures.
-
Recycled card labels.
-
Recycled paper for brochures.
More information at www.grupooroel.com