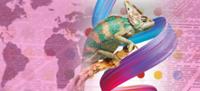
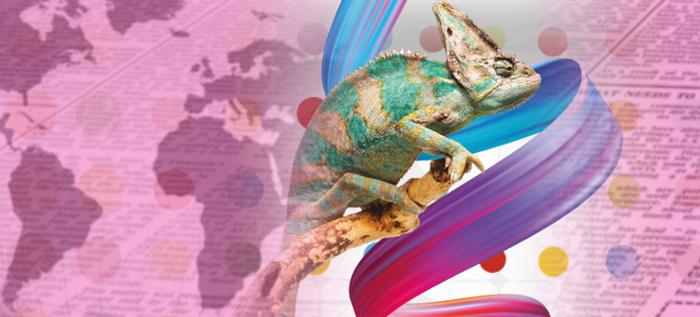
La ingeniería de impresión 3D industrial aplicada a la fabricación de llamadores como ‘souvenir’

La empresa Ingeniería 3D Digital, que trabaja para sectores como el aeroespacial, desarrolla modelos 3D de fundición con gran calidad de acabado que se están utilizando para la reproducción escalable de objetos representativos de hermandades como llamadores de pasos y escudos
Alianza entre la impresión 3D de calidad industrial y la fundición artesanal para unir tradición e innovación a la hora de producir símbolos de hermandades cofrades o rocieras que exhibir en casa como elemento ornamental e identitario, por ejemplo reproducciones de los escultóricos llamadores creados para que los capataces, con el sonido de su martilleo, indiquen a los costaleros levantar o arriar el paso. A ello está aportando sus capacidades la empresa sevillana Ingeniería 3D Digital. Su principal actividad es la fabricación aditiva para las necesidades de sectores como el industrial, el aeroespacial o el agroalimentario, como puede ver quien visite su web www.ingenieria3ddigital.es .
Reproducción en 3D del llamador de la Hermandad de la Paz.
Ingeniería 3D Digital tiene entre clientes a empresas industriales y tecnológicas de muy alta exigencia como Airbus, Heineken, Indra, Alter Technology, Pioneer, Persán, entre otras. Con sede en el Polígono Industrial Calonge, ofrece servicios de 3D en diseño, en escaneado y en impresión. Incluyendo servicio de impresión online para industrias. Su plantilla está formada por ingenieros y técnicos especialistas en fabricación mecánica que han ampliado sus capacidades hacia el manejo de los modernos software de diseño industrial y las técnicas de fabricación aditiva. Todo ello encuentra sinergias con las demandas de los profesionales del arte sacro para elaborar piezas de las que hacer una sola unidad, o replicarlas para su comercialización en serie.
En la fundición, realizado en cubrimiento del modelo en la caja del molde, el fundidor comprime la arena y genera los canales de vertido por donde circula el metal líquido. Al finalizar el proceso se rompe el molde y se repasa la pieza, eliminando las imperfecciones.
Las tres fases del proceso de modelado y fundición
David Serrano, ingeniero de fabricación activa y miembro del equipo de dirección de Ingeniería 3D Digital, explica el proceso de fabricación mediante impresión 3D y fundición: “Se realiza a partir de fotografías, dibujos o bocetos proporcionados por las propias hermandades. Los modelos 3D han sido diseñados mediante software de modelado tipo orgánico. Se utiliza el diseño orgánico cuando buscamos contornos irregulares y caprichosos, basados en trazos y curvas no regladas, y que a diferencia del diseño mecánico, está indicado para creaciones de objetos, personas, esculturas. La fase de diseño es una de las más importantes. Para comenzar, hay que hacer un pormenorizado estudio de la geometría del llamador o del escudo. Teniendo en cuenta que las piezas finales serán fabricadas por moldeo en arena, las superficies que dibujan los relieves y demás ornamentos tienen que tener los ángulos adecuados de desmoldeo para que el proceso pueda llevarse a cabo”.
La impresión 3D en resina produce modelos de altísimos detalles que, junto a un diseño apropiado, permiten utilizarse como modelos para fundición. En la imagen, las figuras del llamador del paso de la Virgen Macarena.
La segunda fase es la obtención de los modelos de fundición por impresión 3D. “Para fabricar una pieza en fundición, es preciso disponer de un modelo con el que hacer el molde de arena. Para la fabricación del modelo de fundición, se ha elegido entre otras tecnologías posibles la impresión 3D FDM. La meticulosa programación de estas impresiones han ayudado a obtener piezas de calidad, con una rugosidad superficial mínima”.
Diseño en 3D del llamador de la Hermandad del Sol.
Y la última fase del proceso es la fundición propiamente dicha. “Con la ayuda del modelo, el fundidor fabrica el molde en dos partes independientes. Para ello utiliza una arena tamizada, con una granulometría muy fina, capaz de copiar los detalles más pequeños e intrincados del modelo. Realizado en cubrimiento del modelo en la caja del molde, el fundidor comprime la arena y genera los canales de vertido por donde circulará el metal líquido. Cerrando ambas partes, se cuela la fundición rellenando la oquedad interior con la forma del modelo, extraído previamente. Al finalizar el proceso se rompe el molde y se repasa la pieza, eliminando las imperfecciones. El resultado son piezas de gran calidad, con detalles de muy buen acabado que serían muy difíciles de lograr de forma manual”, detalla David Serrano.
Los 62 escudos fundidos en hierro para Villamanrique
Otra aportación muy interesante desde Ingeniería 3D Digital, por innovación y por repercusión, ha sido la fabricación de 62 escudos de las hermandades rocieras que pasan por Villamanrique de la Condesa durante la romería. Encargo del ayuntamiento de dicho municipio para situarlos con finalidad ornamental y simbólica en el bulevar de la nueva Avenida Paso de Hermandades. En esta ocasión, se utilizó un modelado 3D tipo orgánico, propio para el diseño de elementos ornamentales, contornos y formas naturales. David Serrano comenta: “A quien diseña esto con software se les reconoce como 'escultores digitales', quién sabe si representará un nuevo oficio de importancia para el sector del arte sacro. Este trabajo supone sustituir las labores de escultores, orfebres, etc. a nuevas técnicas digitales acortando tiempos, y tecnificando los procedimientos. Por ejemplo, las técnicas de repujado ven en el esculpido digital la posibilidad de escalado del modelo de una forma inmediata, ahorrando tiempos y reduciendo defectos e inexactitudes. Si bien hay quien puede rechazar estos métodos por perder la característica artesanal, habría que considerar que el diseñador, o escultor digital, posee una formación artística. Se trata, más bien, de una transformación de los procedimientos y métodos tradicionales”.
Los diseños 3D de los escudos debían diseñarse desde fotografías aportadas por las propias hermandades. “Además, debían resultar con una forma tal, que permita su utilización para el moldeo en arena. En palabras de los fundidores, el modelo debe tener los ángulos apropiados para el desmoldeo. Una vez obtenido el diseño 3D digital de los escudos, se procedió a su fabricación mediante impresión 3D. Estas técnicas permiten reproducir fielmente el diseño 3D físicamente en material plástico, que más tarde será utilizado como modelos para fundición. Los modelos para fundición impresos en 3D son una suerte de 'master' con el que el fundidor realiza los moldes sobre el que verter el metal fundido. En este caso, se utilizó moldeo en arena y fundición de hierro. Una vez solidificado el metal, se destruye el molde de arena, se extrae la pieza limpiándose de restos de arena e impurezas y se cortan los canales utilizados para llenar la cavidad del molde”, pormenoriza David Serrano.
INFORMACIÓN: ElCorreoweb.es